Sharing some failure mode analysis with others who has been inside the battery pack (NOTE : HV can be deadly dangerous so absolutely need to be familiar with all HV protection precautions) This is @mr_hyde car with his original post here and here.
Car is 2014 MS P85D 67k miles. In Seattle always (no salted roads, rains frequently but low humidity otherwise) @mr_hyde is 2nd owner acquired recently.
Car disabled with BMS_F107 (Cell sensor voltage code) Thought it might be a loose voltage sensor wire but found the following after pack opening
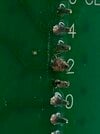
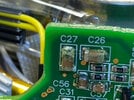
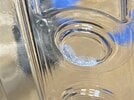
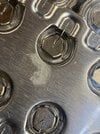
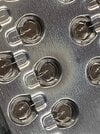
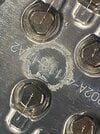
These condensation patterns suggest the following failure mechanism
Car is 2014 MS P85D 67k miles. In Seattle always (no salted roads, rains frequently but low humidity otherwise) @mr_hyde is 2nd owner acquired recently.
Car disabled with BMS_F107 (Cell sensor voltage code) Thought it might be a loose voltage sensor wire but found the following after pack opening
- No evidence of broken seals for water ingress anywhere (pack cover lid, front hump, fuse cover)
- No evidence of coolant leak from any pipe fittings (no silicate residue or sticky coolant residue anywhere)
- All umbrella valves looked fine without failed seal
- Condensation evidence in the modules under the hump and first 3+ rows of modules from front. Rear 3+ rows looks perfectly fine.
- Spore shape slightly hazy white patterns around few 18650 cells. This is likely due to corrosive electrolyte release. Perhaps this is fairly common for 18650 cells? The big shiny electrode plate captures the evidence easily. 18650 manufacturing process shows electrolyte fill ( link ) and drying ( link ) process. Not too concerned about this. Perhaps occurred early on after module + plastic cover assemebly.
- Top plastic cover on modules have dime size indents that rest on top of electrode plates (for fitting) Many of these show condensation marks.
- Long run sections of plastic cover touching the electrode plate shows signs of dried water flowing marks.
- Tiny droplets of dried water marks on parts of the electrode plate not contacting the plastic cover.
- BMB’s C26/C27 (Rev 1.5 on this car, later BMBs might have redesigned this area) are the tallest component on top of the circuit board and very close to (probably contacts) the bottom plastic tray cover. 4 BMBs shows corrosion here. Also voltage sensor wire's solder pins on module #9 (upside down mounted compared to the rest) show corrosion. There are 2 potential failure mechanisms. Conformal coating is likely sprayed on and side walls of the caps and vertically standing solder pins would have a weak / no coating layer. Also potentially conformal coating was rubbed off from contact+vibration and/or condensation formed here which eventually corroded the solder points.
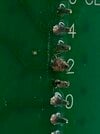
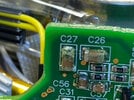
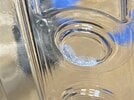
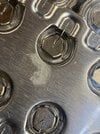
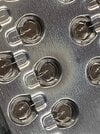
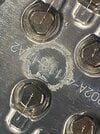
These condensation patterns suggest the following failure mechanism
- Since all failures are near the front of the pack and vent port is on top of the hump. It seems likely as the pack “breathes” (1000 lb of warm pack cooling will draw in external air from the vent) moist air is potentially drawn into the pack
- Vent is on top of hump which is where some windshield water run off dumps on. Furthermore, AC drain (even improved to dump further forward of the pack) dumps nearby. Usually the hump and anything ferrous in the area (DCDC box on this 2014 MS) shows evidence of water dump + rust/corrosions in most cars that has seen salt road or rain or carwash often.
- Place desiccant bags inside the pack prior to resealing the pack. Most available space is near where coolant enters the pack
- Drill and install bottom serviceable desiccant cartridges like Smart Car EV ( link ) again near the coolant pack entry area.
- My understanding is the Rav4 EV and MB B-Class (both built with variation of Tesla drive unit and battery modules) both have serviceable desiccant bags/cartridges and maybe a circulating fan?
- Another possible solution is to remove the vent port and extend it along with an inline drying box filled with desiccant bags. However, the frunk box might be in the way for RWD cars.
- This is less frequent failure than water ingress through rusted fuse cover in salted road area cars. But this seems likely to occur over time depending on humidity in the region.
- Accumulated water condensation on the electrode plate can theoretically damage the ultrasonic cell welding connections in nearby cells. But maybe BMB’s capacitors will fail first such as on this pack. But on later BMBs with different designs, not sure this will be true.
- Will Tesla reman effort go though this level of detail to inspect all 16 BMBs? This car failed with 1 BMB (ScanMyTesla showed module 8 - note module #s reflect network ordering and IS NOT the HV serial bus order which zigzags serially from the rear. This is a potentially dangerous misunderstanding when disassembling the pack. Removing the fuse breaks the serial HV chain into 14x and 2x modules. Not split into half. Many people misunderstand this from network module # ordering) But 3 others were just behind this haven't yet completely failed. If just go by diagnostic tool directed inspection, 3 near failed BMBs would have remained in the pack.
- Opening the pack lid non destructively is a PITA and can easily be 10-20 hours (remove carefully, clean off all sealant residues, hammer lid sealant surfaces flat etc.) @250/hr labor rate easily $3-$5k cost. Perhaps can go faster with developed tools with experience. Chevy Bolt uses a rubber gasket with bolt spacer sleeves to provide proper even pressure. This guy did it in his wheel chair ( link ) Bolt also has full service manual on disassembling inside the pack and I presume supply all parts.
Last edited by a moderator: