Back to the DIY seat install. This is the wrap up.
The indy body shop installed the rear crossmember with same-day service, once the part arrived from Tesla.
They charged me $125 for the part and 3.8 hours @ $48/hr for $315 total with taxes. It was clearly the first time they did this job, so is probably longer than an experienced tech would take, but their hourly rate is way less than Tesla, so I wasn't bothered by it.
All the wiring was in place for the liftgate switch. All my trim was pre-scored for the strikers and seat attachments, so I didn't need the templates, or to measure anything (except for the location of the switch - see below).
I also added two new high-brightness LED lights using the existing trunk lighting wiring, just had to finish cutting the pre-scored light openings in the trim and pop the lights into place. This is the sort of "freebie" you get to do when you DIY
The parts I needed from the list in the service bulletin were just these:
(this depends on what you transfer with the seats - try to get the left and right strikers as they are pricey).
(Strikers are correct part number for my 2015 that falls within the "new rear node" also called "2nd generation rear node")
ASSEMBLY - HIP STRIKER LEFT 1013626-00-D $97.30
ASSEMBLY - HIP STRIKER RIGHT 1013629-00-D $97.30
SWITCH FOR 3RD ROW SEAT w/ POWERED LIFTGATE 6008902-00-A $22.00
BARREL NUT, M10 2006869-00-A $3.60 (Qt 2)
BOLT, TORX, M10x28.4 1022449-00-A $0.59 (Qt 2)
BOLT M8x20 WITH MAT POINT 1014747-00-B $0.22 (Qt 4)
These two parts cover the cuts you have to make into the back of the second row seats to expose the existing latch mechanisms hidden in the back of the seats. I spend some time feeling to make sure the latches were there, and made a single slit to inspect before going to town cutting the openings. I had to trim the plastic of the bezel slightly with my pocket knife to get these bezels to fit tightly. It definitely looked like the upper and lower parts came from different runs - one had new packaging, the other had faded packaging.
2ND ROW BEZEL UPPER 1013633-00-A $2.00
2ND ROW BEZEL LOWER 1014277-00-A $2.00
The "Headrest Latch cover" and M4 screws were not needed, as those parts were already attached to the seats I was using. The 8 M10 nuts were also not needed - I believe these are used to hold the crossmember in place, but the body shop did that part.
I did break two of the "Heart Flex Clip with Washer" (aka door panel clips) that hold the rear trim in place - I had bought a dozen to have, so it was no big deal - 1025401-00-A $0.22 each.
The C-pillar trim panel that holds the liftgate switch is very backordered, and the SC wasn't very hopeful about it, so I just carefully cut a rectangular opening for the switch in my existing trim. It has the proper recessed space for the switch, just needs to be cut. The switch has a clip on the back that holds it in a panel behind the trim, so getting the opening in the trim to line up with the place it clips into was harder than usual - I lined it up by using my laser line level (normally used for carpentry) to establish a line with the trim removed, then fit the trim in place and transferred the marks. To double check, I stole a can of play-dough from my kids and pushed it into the recess to make an impression of the space. In the end, I was within a couple of millimeters and just had to extend the opening a little bit on one end.
-THE END-
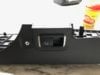